効率改善事例【製造ライン】
的を得た着眼点とアイデア、それと根気で成し遂げる。
以下は、弊社が行った改善の中で、特に効率改善に寄与した事例(ロスの低減と設備能力の向上)です。
特別に技術を要するものではなく、的を射た着眼点とアイデア、それと根気で成し遂げたことが特徴です。
大抵の工場では、新規設備を立ち上げる場合、技術者(社内の生産技術者や社外の設備メーカー)は、稼働率70%もいって、 『まずまず流せる』レベルになれば帰ってしまいます。これを90%以上にするのは現場の仕事です。
『あるべき姿の追求』をキーワードに、地道な活動で効果を上げる。その為には、前述した程度の基礎知識があれば十分なのです。 ただし、世間の多くの人材業者は、この基礎知識すら持っていません。ただ言われたことをこなすだけです。 弊社は基礎教育を行っているので、以下の改善ができました。
■改善事例1/全体のサイクルタイムを支配していたステーションの発見と改善
ラインの中で、最もスピードが遅く、全体のサイクルタイムを支配していたステーションをつきとめ、その各アクチュエーターの 動作を以下の方法で速くした。
1 エアーシリンダーのスピコン調整にて速めた。
2 障害物をよけて迂回動作をしていたロボットに対し、障害物を移動させて迂回を無くした。
![]() |
![]() |
![]() |
■改善事例2/チョコ定部位を改善し効率アップ
設備の立上げ設置精度が悪く、チョコ停の多発していた部分に対し、やすりでボルト穴を広げて調整しろをつくり、あるべき寸法位置に位置合わせを行い、チョコ停をなくした。
■改善事例3/芯だし治具を自作し効率アップ
芯だし治具を自作し、すばやく正確な芯だしを行った。
![]()
|
![]() |
![]()
|
■改善事例4/セル生産方式で効率アップ
セル生産方式で効率を向上させた。
![]() |
![]() |
![]() |
まずA作業をまとめて行い、中間仕掛りを 大量につくる。その後B作業を別に行い、 製品を仕上げる。 | AとBの作業を一度に、一箇所で行った。 ① 取り置きの動作が無くなり時間短縮。 ② 中間仕掛りがなくなり、リードタイム短縮。 ③ パレット2枚分の空きスペースができた。 |
■改善事例5/載せ換え作業をなくし効率アップ
部品を運搬してはパレットに載せ変えていたところをパレットを廃止し、台車のままストックすることで載せ換え作業をなくした。
■改善事例6/作業配置を変えて効率アップ
機種毎の運搬台車について、頻度の高い機種の台車を最も効率の良い位置に交換することで、 余計な歩行時間を削減した。
![]() |
![]() |
![]() |
2階から返却された空箱を仕分ける作業。 コンベアーのすぐ脇で、最も効率の良い場所に 長期停滞品がおいてあった。 最も数の多い機種の空箱は図中①の場所。 |
最も頻度の多い①台車コンベアーのすぐ 横に置くことにした。(制御盤前だが、台車 なので、簡単に退かせる) 長期滞留品は 遠くに離し、2番目に頻度の多い②台車をその場所に配置した。 |
■改善事例7/一部自動化を取り入れ、作業密度を高め効率アップ
手待ちの多い工程を改善して一部自動化すると同時に、別作業をコンパクト化して追加させ 一人当たりの作業密度を高めた。
![]()
|
![]() |
![]()
|
||
![]()
|
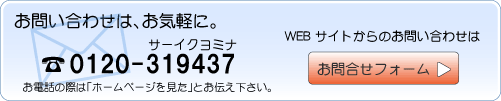